They miss nothing. The experts at the Munich-based high-tech company TOPseven make inspection drones so smart that the flying eagle eyes immediately spot damage to rotor blades. And they do so almost autonomously and according to a fixed flight plan.
On-site visit Brandenburg. A wind farm on the outskirts of Berlin. Open spaces, large towers, deserted. A gentle breeze lets the blades turn comfortably. Only one turbine stands still. A camper van in front of it. Drug dealing? Mafia hangout? You could be thinking of a filming location for a crime thriller. But instead of money and weapons, information is collected here. And it’s completely legal, with permission and most welcome.
A six-armed inspector
Katja Weißbach is already waiting for us. She is responsible for sales at TOPseven. She immediately corrects our expectations: “We don’t design drones and we’re not full-time wind turbine service technicians. TOPseven sees itself as a software development company. Among other things, for automated flights of inspection drones. Hence our motto – Making Drones Smarter. Not just for wind turbines, by the way, but also for solar systems. We want to simplify inspections wherever structural inaccessibility makes it difficult.”
In order to make the multi-winged devices really smart, in-depth knowledge of both wind turbine generators and drone technology is of course required. Katja Weißbach has therefore organized competent reinforcement. Christian Minnieur and his son Pascal are responsible for training service technicians at TOPseven, among other things. They are given several days of training to prepare them for using the flying eyes. Even for experienced hobby drone pilots, the professional devices are a completely new challenge. TOPseven works with several of these training teams throughout Germany.
Monitoring via autopilot
Christian Minnieur has already prepared the black DJI Matrice 300 RTK. Before the six-armed aircraft takes off, the technicians have set up a tripod that enables data to be transported from the drone to the base station without an external radio network and allows the drone to fly with centimetre precision. The optical system consists of a specially developed 61 Mp TOPseven camera. The high resolution makes it possible to visually detect even the smallest damage to rotor blades.
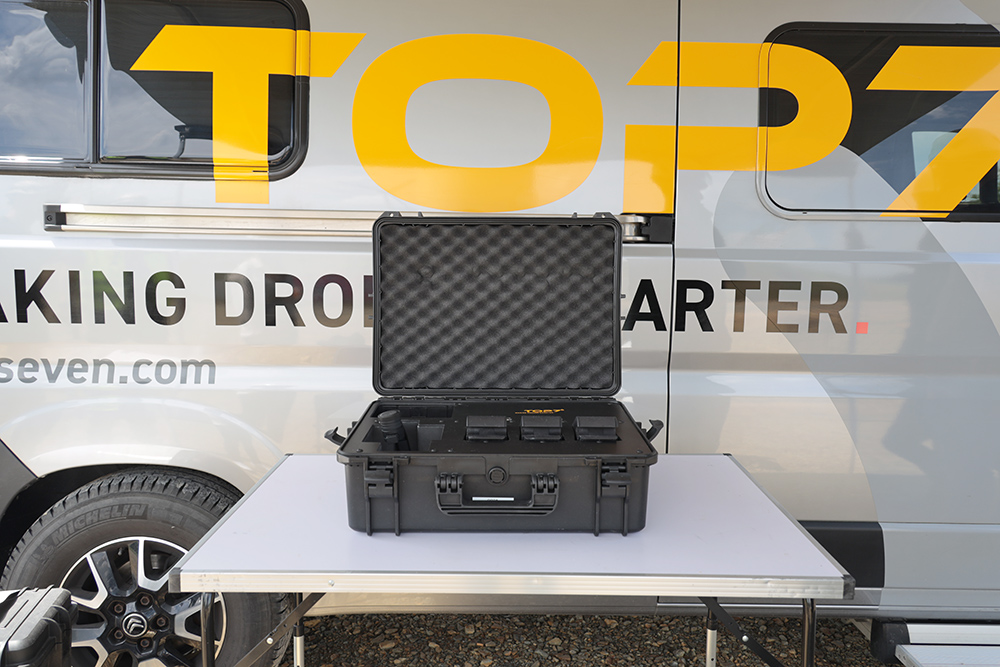
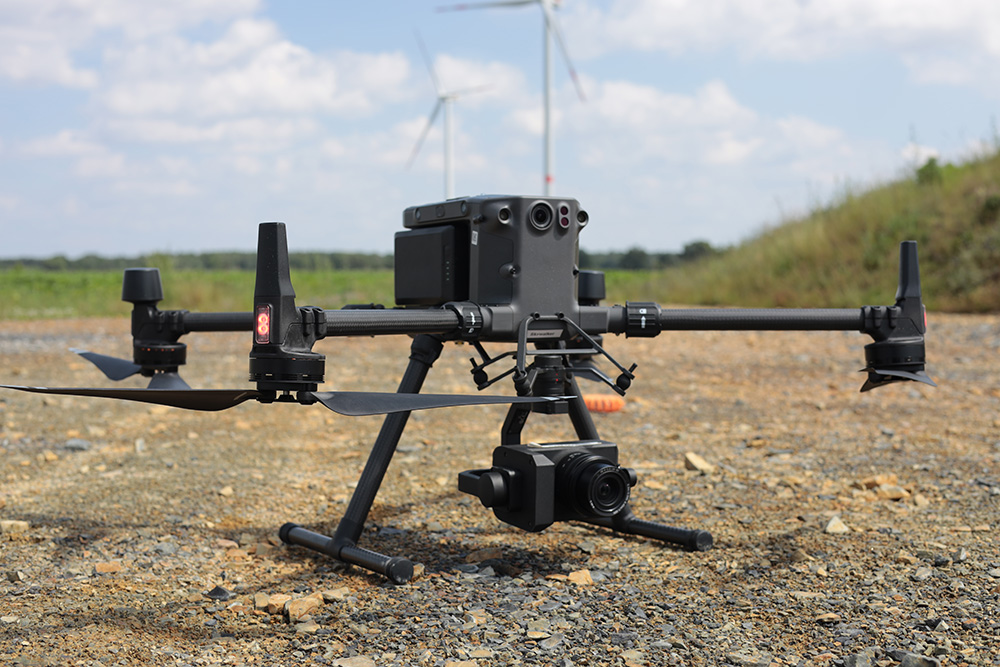
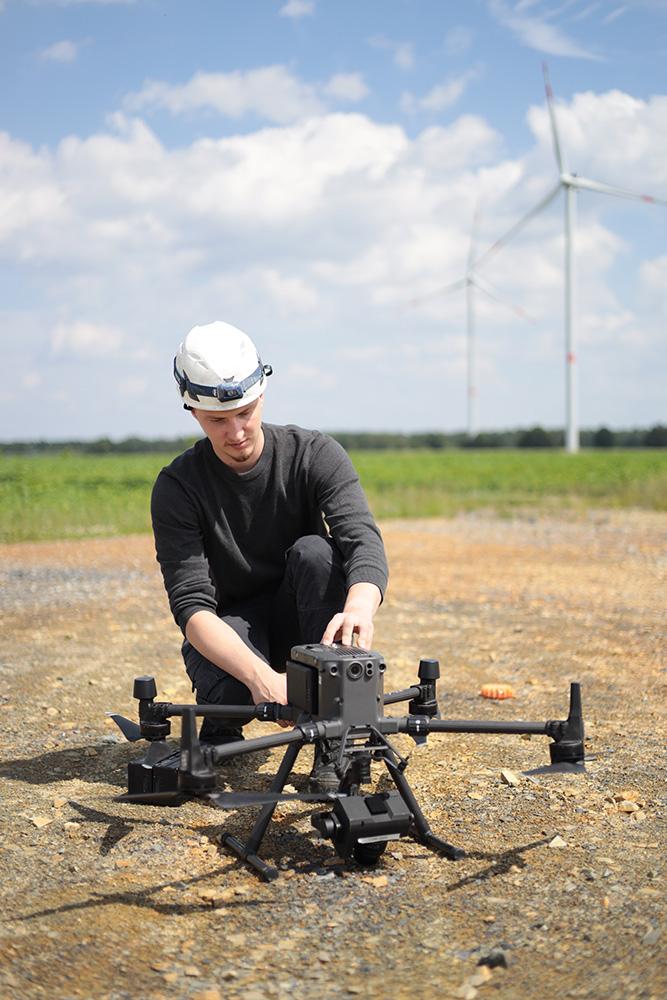
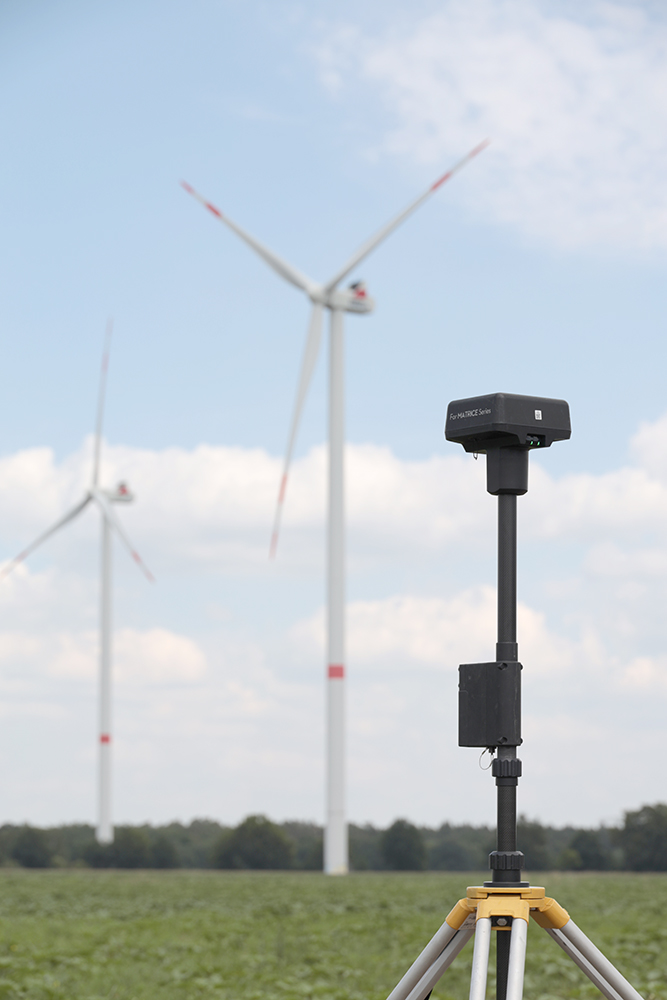
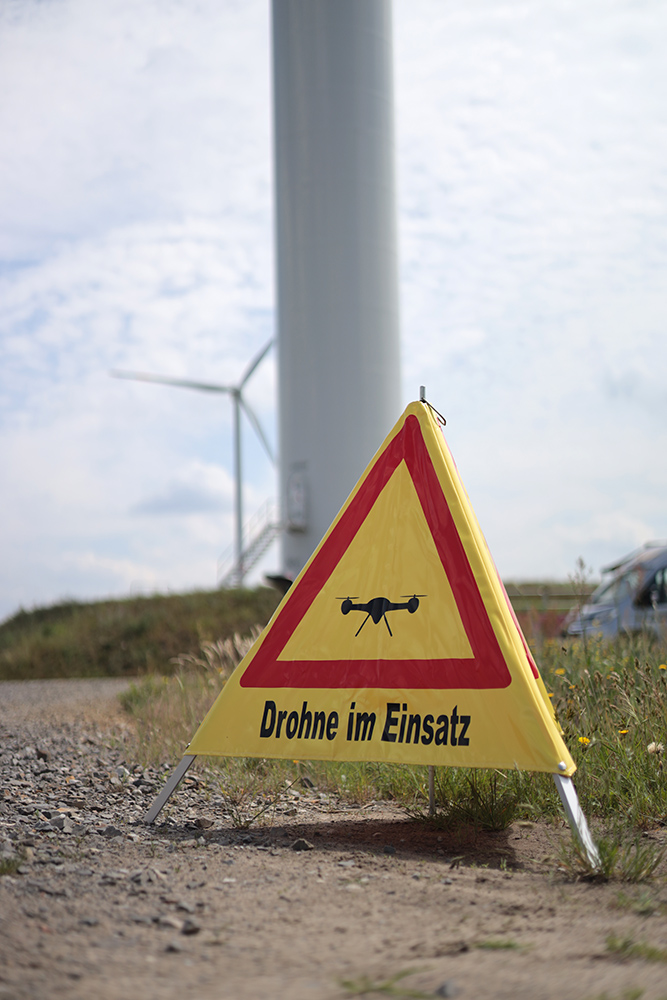
However, it is not only storms that stress wind turbine generators. Heavy thunderstorms, including lightning strikes, also leave unwanted traces. As a rule, the lightning is captured on the blade by special receptors and the lightning energy is dissipated via the lightning discharge path. Phoenix Contact has developed its own sensor technology to measure lightning currents in the discharge path and thus detect damaging strikes. However, these systems have to be checked every two years. TOPseven has equipped its flying detectors with special sensors for this purpose. The signal generators are connected to the lightning protection cable in the rotor blade root. This has to be individually adjusted from turbine type to turbine type. The drone itself has a field sensor. The generators then send signals to the lightning discharge path. The drone flies over the blade starting from the tip and receives these signals. In this way, any damage can be detected with centimeter precision. The flight routes are precisely defined and the drone flies them autonomously. “With this data, the operators can precisely localize the damage and then repair it much faster than if the entire plant had to be inspected,” explains Katja Weißbach.
Expensive tests
Photographer Andre Köller enthusiastically takes his own drone out of its case to follow the black DJI Matrice into the air to take pictures. The team looks on with amusement at the tiny aircraft next to the professional device. The take-off of the two aircraft still requires one pilot each. Then they part ways as the service drone sets off on its predetermined route. The Vestas 136 has a hub height of 149 meters, so the DJI must also reach this height. Christian and Pascal Minnieur follow the flight on the computer, which is now receiving the flight data. The drone flies its mission autonomously.
For Henri Fröhlich, the scenery is already part of everyday life. “We’ve been working with TOPseven for a few years now and make our system available for the necessary tests.” Fröhlich is technical operations manager at Notus Energy Service: “We install and maintain wind power and PV panels. We even operate the Vestas here ourselves. This makes it less complicated if the wind turbine has to be shut down for the further development of the inspection software.” The system is normally checked monthly. The nacelle is serviced every six months and the lightning protection is checked by the manufacturer every two years.
Innovations for wind power
The development of drone control is also no small matter in organizational terms, because if the blades are at a standstill for tests, no electricity can be harvested or sold. Compensation payments are usually due. But thanks to the tests, the operator of this turbine can be sure that his wind turbine is in top condition. And not only in the area of maintenance: “We have also installed a bat detection system on this turbine. If the fluttering creatures start visiting the neighboring forest, the turbine shuts down automatically,” says Fröhlich, explaining the special innovation on “his” Vestas.
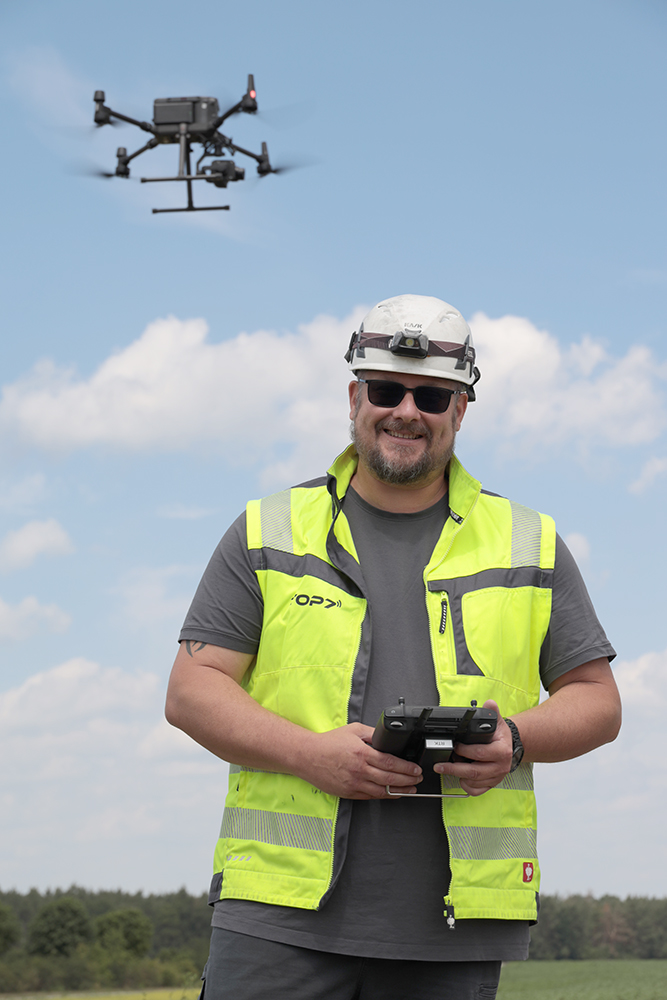
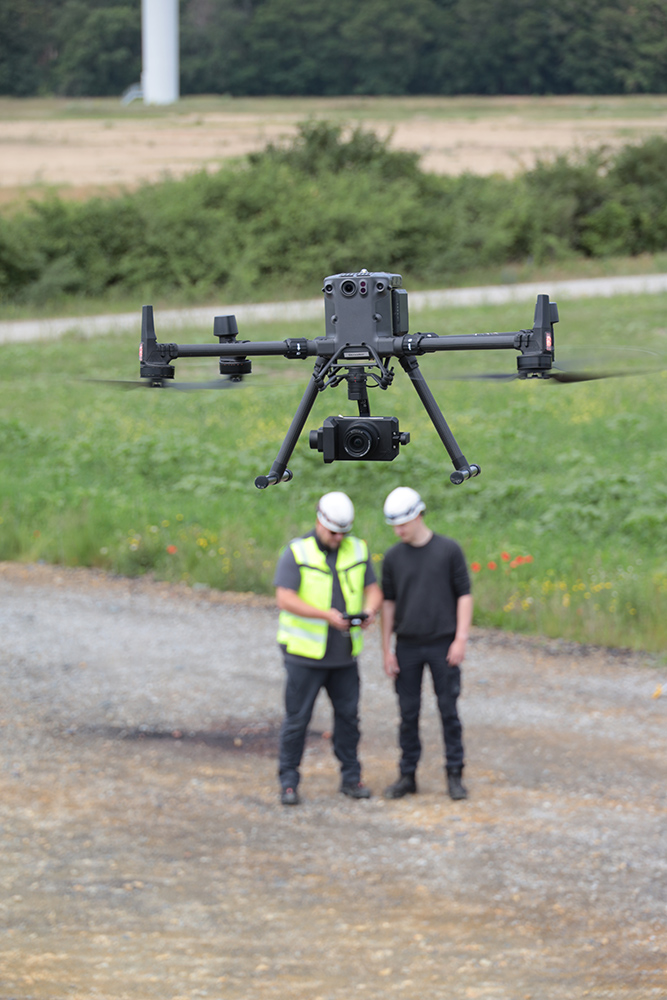
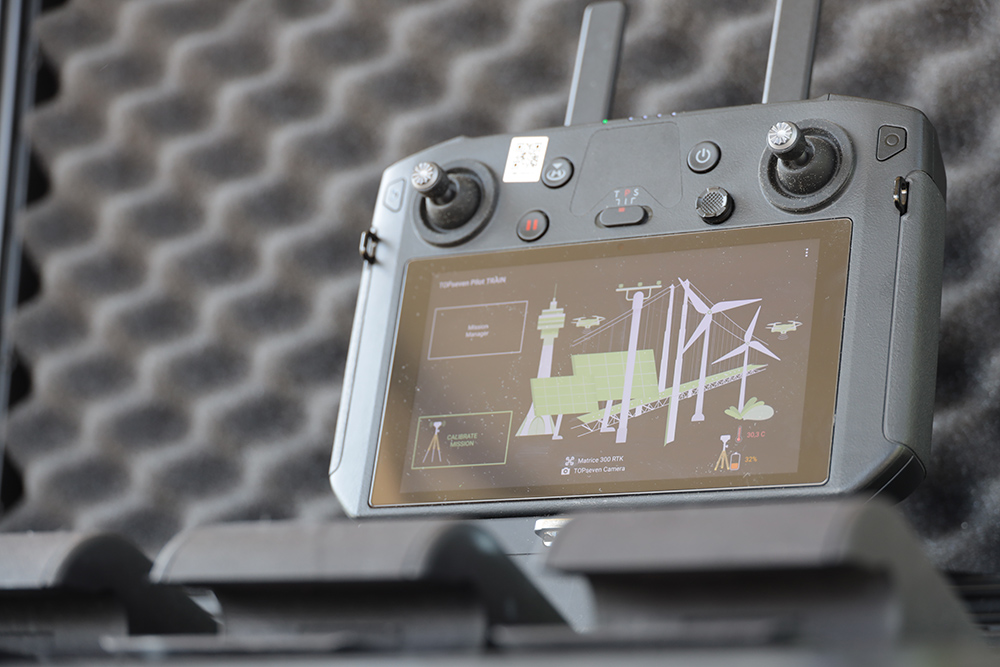
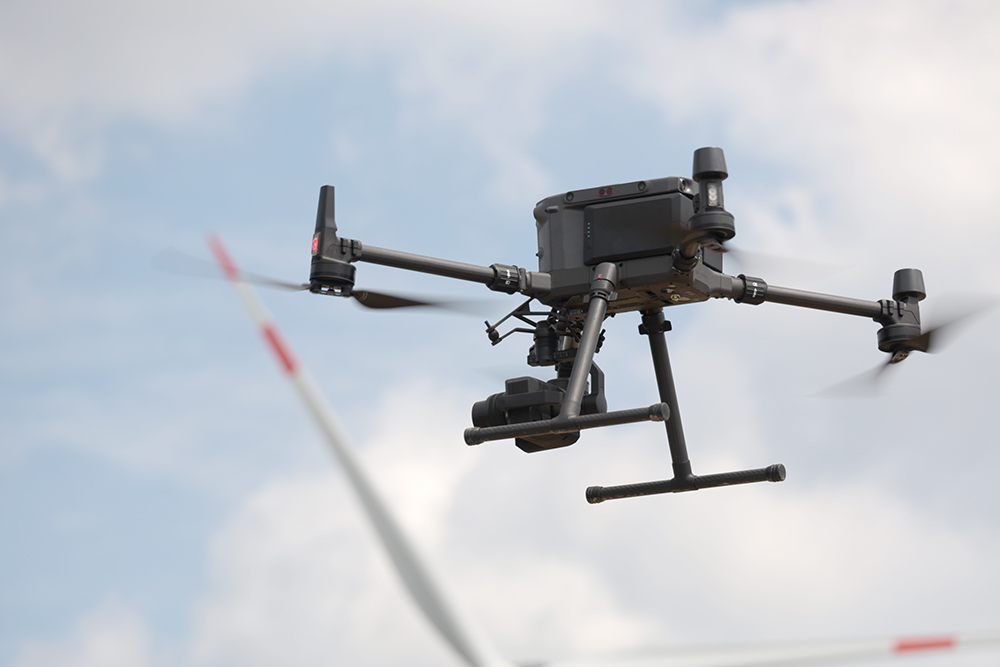
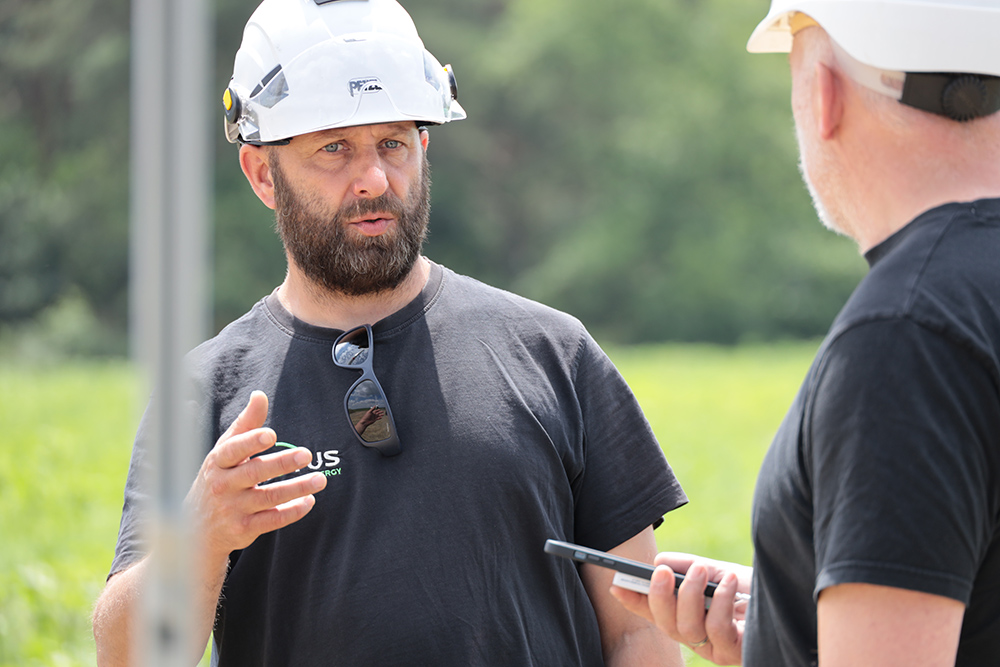
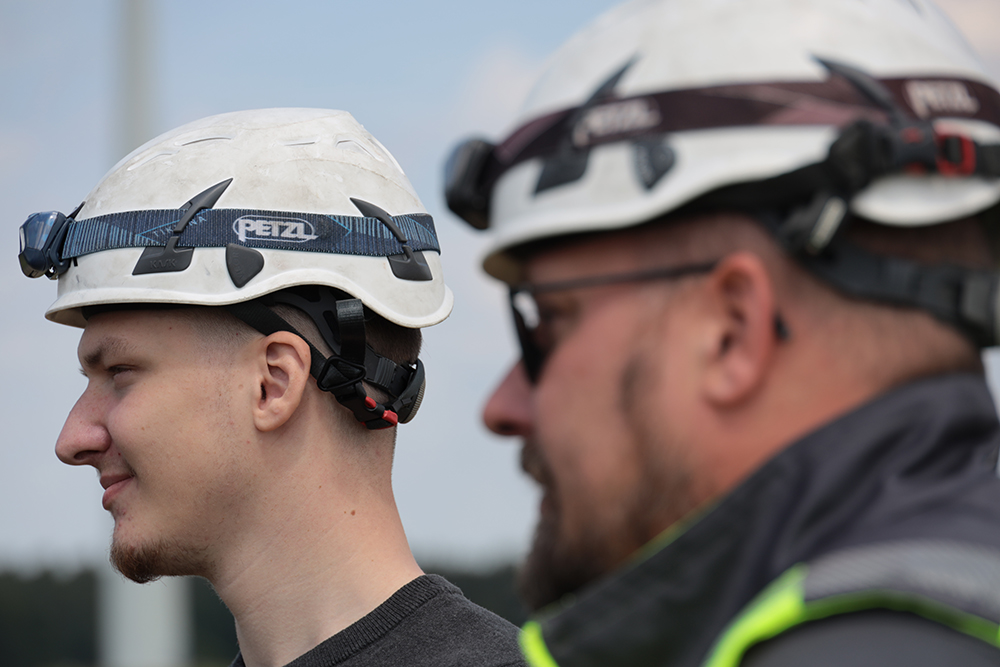
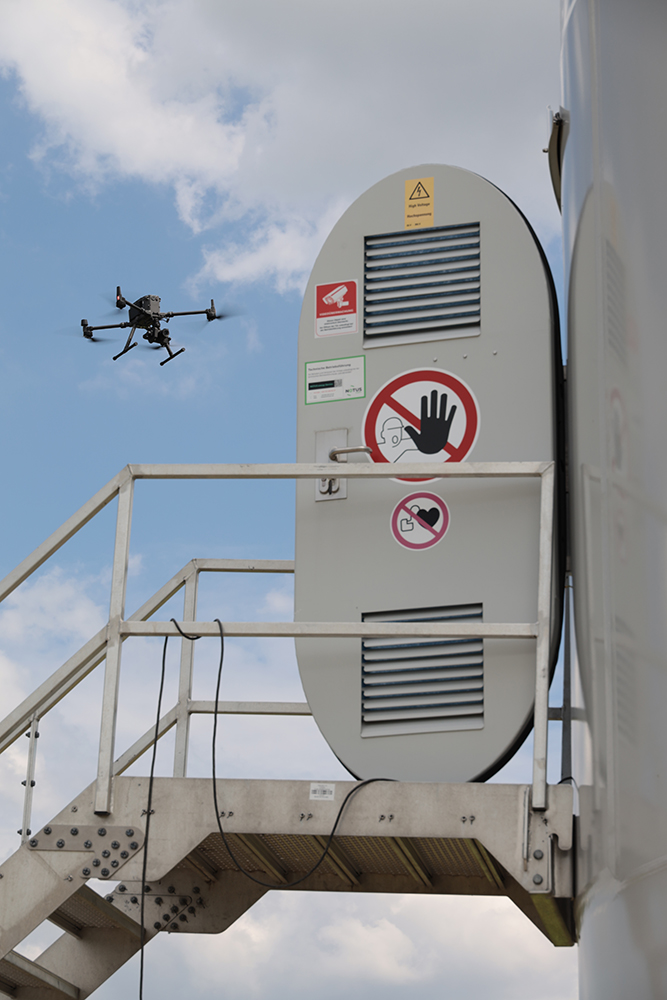
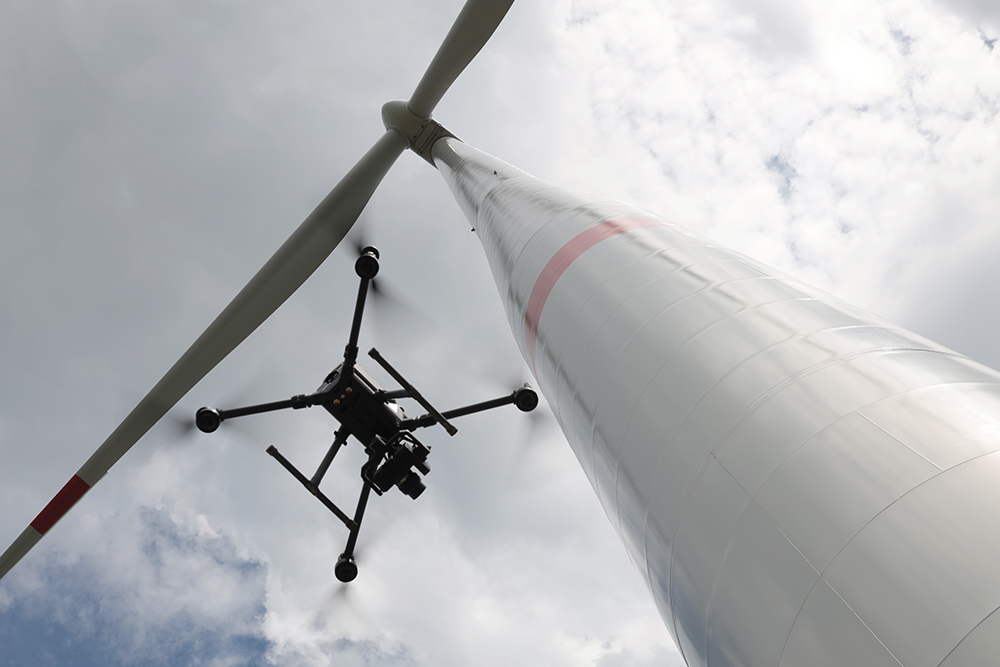
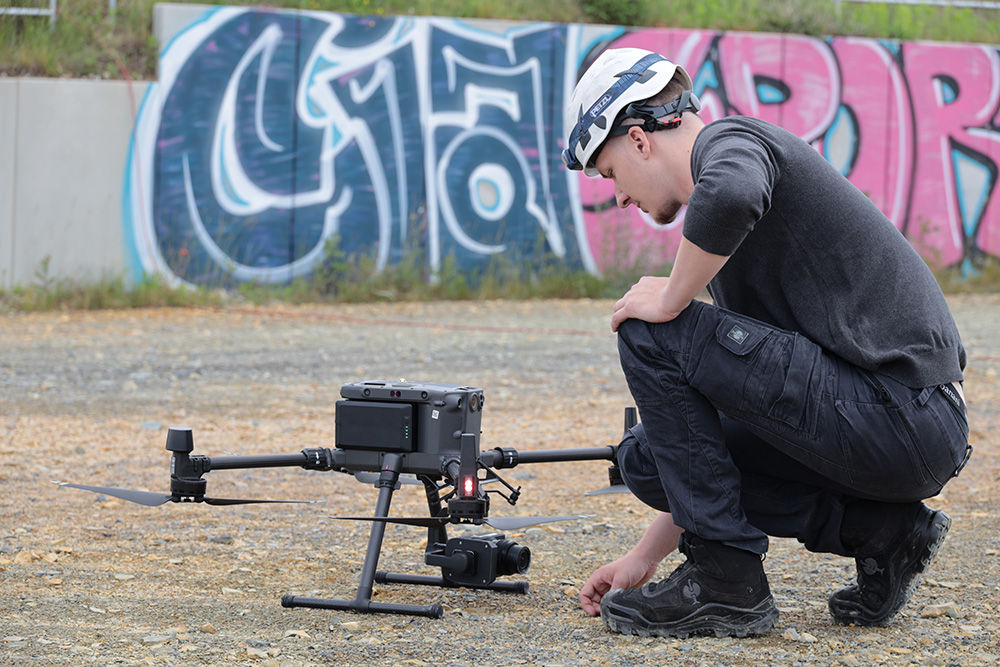
While the drones begin their landing approach and are caught again by their pilots, Fröhlich heads for the windmill. Flight completed – standstill over. The optimally controlled turbine should start turning again. And in the van, the laptops are closed and the data is collected. Slowly, the blades of the Vestas resume their rotation. And when the team trolls off, the wide open field outside the gates of Berlin is quiet again.